The Tinplate Laminating Line is a cutting-edge technology that has transformed the metal packaging industry. By bonding polymer films directly onto tinplate (or tin-free steel), this process creates laminated steel, a superior material for food and beverage cans, aerosol containers, and more. Unlike traditional methods where coatings are applied after can formation, laminated steel integrates the protective layer at the steel mill level, ensuring enhanced durability, corrosion resistance, and aesthetic appeal.
One of the most advanced applications of this technology is seen in high-speed laminated steel production lines in Thailand, which cater to the growing demand for eco-friendly and high-performance metal packaging solutions.
What is Laminated Steel?
Laminated steel, also known as film-laminated metal, is produced by fusing a thin layer of polypropylene (PP) or polyester (PET) film onto tinplate or tin-free steel through a high-temperature pressing process.
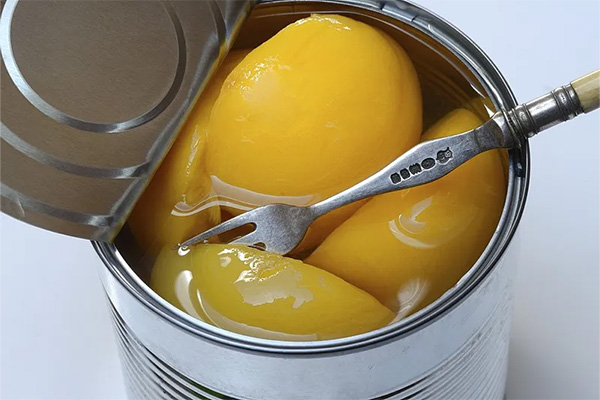
Key Advantages of Laminated Steel
- Superior Corrosion Resistance – Ideal for acidic food products like tomatoes and carbonated beverages.
- Enhanced Durability – Resistant to scratches, abrasion, and deep drawing stresses during can manufacturing.
- Eco-Friendly & Safe – Eliminates the need for solvent-based coatings, reducing VOC emissions.
- Aesthetic Flexibility – Offers glossy, matte, or textured finishes for premium branding.
The Tinplate Laminating Line: Core Technology & Process
The heart of laminated steel production lies in the Tinplate Laminating Line, which consists of precision machinery designed for high-speed, high-efficiency film application.
Key Components of a Tinplate Laminating Line
- Surface Treatment Unit – Prepares the metal surface for optimal film adhesion.
- Film Feeding System – Precisely aligns and feeds the polymer film onto the metal sheet.
- Thermal Lamination Unit – Uses heat and pressure to bond the film permanently.
- Cooling & Inspection Section – Ensures uniformity and detects defects before rolling.
Why High-Speed Laminating Lines Matter
Modern Tinplate Laminating Lines, such as those deployed in Thailand’s high-speed laminated steel production facilities, can process over 200 meters per minute, making them ideal for large-scale packaging manufacturers. These lines reduce production costs while maintaining exceptional quality standards.
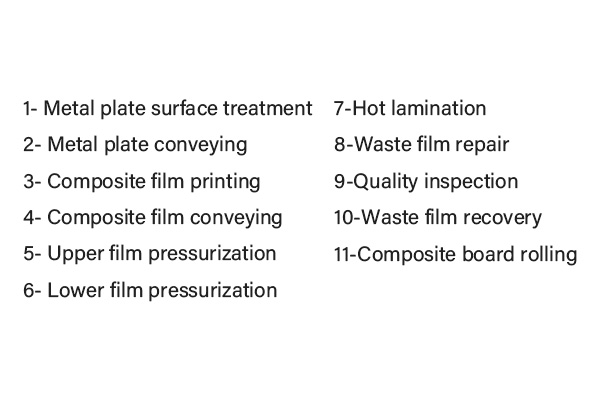
Case Study: High-Speed Laminated Steel Production in Thailand
Thailand has emerged as a key hub for advanced metal packaging solutions, with several manufacturers adopting high-speed Tinplate Laminating Lines to meet global demand.
Benefits of Thailand’s Laminated Steel Production
- Cost Efficiency – Lower operational costs compared to traditional coating methods.
- Sustainability – Reduces chemical waste and energy consumption.
- Export Growth – Supplies high-quality laminated steel to food, beverage, and industrial markets worldwide.
A leading Thai manufacturer recently installed a fully automated Tinplate Laminating Line, achieving a 30% increase in output while maintaining zero-defect film adhesion. This success highlights the potential of laminated steel in modern packaging.
Future Trends in Laminated Steel Technology
As sustainability becomes a priority, laminated steel is set to dominate the metal packaging industry. Innovations such as biodegradable films and smart coatings (e.g., antimicrobial layers) are being integrated into Tinplate Laminating Lines, further enhancing functionality.
With high-speed laminated steel production expanding in Thailand, manufacturers worldwide can leverage this technology for superior, eco-friendly packaging solutions.
By investing in advanced laminated steel production, businesses can stay ahead in a competitive market while meeting the growing demand for sustainable metal packaging.