Changing Tech Behind Today’s Metal Cans: Laminating Machines Explained
For over a hundred years, we’ve relied on metal containers to preserve everything from grandmother’s face cream to today’s energy drinks. But here’s what most people don’t know – the same basic tin can technology from the 1800s is getting a revolutionary upgrade. Modern laminating machine are completely transforming how we produce metal packaging, especially in fast-growing markets like India where demand for better cans is exploding.
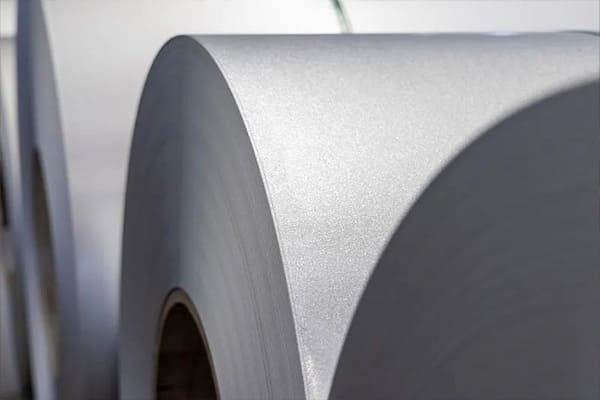
The Historical Journey of Metal Can Manufacturing
The art of can manufacturing dates back to the late Qing Dynasty and early Republic of China era. Classic products like snow cream and mentholatum were packaged in these durable tinplate containers. While modern manufacturing has improved precision and design variety, many fundamental processes remain unchanged from their 19th century origins.
Why Traditional Methods Persist
- Proven durability across generations
- Excellent product protection
- Established manufacturing infrastructure
- Consumer familiarity with metal packaging
The Technological Leap: Laminating Machines Enter the Scene
The breakthrough came in 1989 when Japanese manufacturers developed the first successful film-laminated steel, combining metal strength with polymer versatility. Modern laminating machine now enable:
Feature | Benefit |
---|---|
Electromagnetic induction heating | Precise temperature control (±1°C) |
Multi-layer film application | Enhanced corrosion resistance |
High-speed operation (100-200m/min) | Improved production efficiency |
Customizable film types | Tailored solutions for different products |
India’s Custom Laminating Machine Solutions
India’s packaging industry has embraced this technology with customized laminating machines designed for:
- Spice and food packaging
- Pharmaceutical applications
- Specialty chemical containers
- Luxury goods packaging
These systems incorporate local manufacturing requirements while maintaining international quality standards.
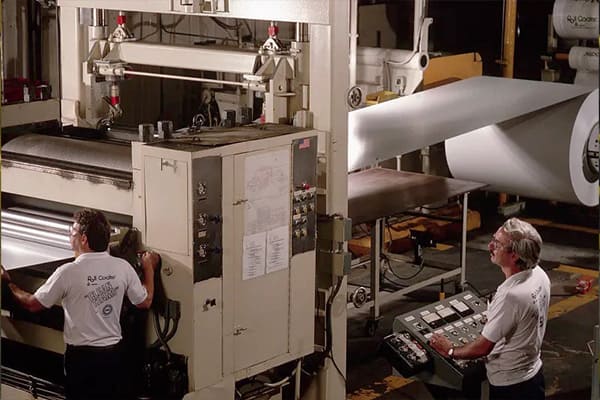
Technical Breakdown: How Modern Laminating Machines Work
Core Components of Advanced Laminating Systems
- Precision Heating System
- Electromagnetic induction rollers
- Temperature stability within ±1°C
- Rapid heating to 250°C+
- Film Application Unit
- Multi-layer PET film application
- Customizable film thickness (12-25μm)
- Specialized adhesives for different substrates
- Quality Control Systems
- Real-time thickness monitoring
- Automated defect detection
- Consistent pressure application
Material Science Breakthroughs
Modern laminating technology utilizes:
- Chromium-plated steel substrates (TFS)
- Modified PET films with enhanced adhesion
- Specialty coatings for food safety
- Custom color and texture options
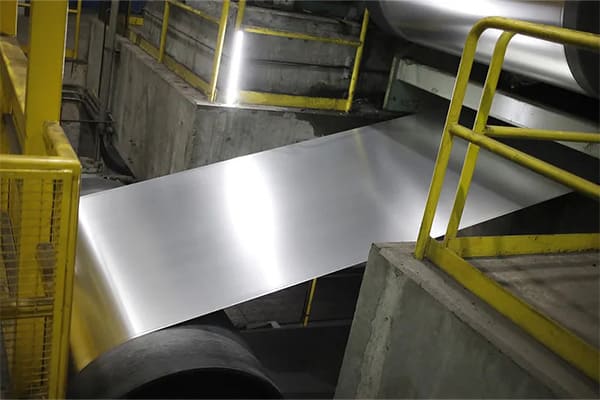
Applications and Market Potential
The global laminated steel market is projected to grow at 6.8% CAGR, with particular strength in:
Food and Beverage Sector
- Canned foods
- Beverage cans
- Ready-to-eat meals
- Specialty food packaging
Industrial Applications
- Chemical containers
- Aerosol cans
- Paint and coating packaging
- Industrial product packaging
Indian Case Study: A Mumbai-based manufacturer recently implemented a custom laminating machine solution that increased production capacity by 35% while reducing material waste by 22%.
The Future of Laminating Technology
Emerging trends include:
- AI-powered quality control systems
- Sustainable bio-based films
- Smart packaging integration
- Energy-efficient heating technologies
As environmental regulations tighten globally, laminating machines offer a sustainable alternative to traditional tinplate production, reducing heavy metal usage while maintaining packaging performance.
Conclusion: Embracing the Laminating Revolution
From its historical roots to modern applications, metal packaging continues to evolve. Advanced laminating machines represent the next chapter in this story, offering Indian manufacturers and global partners alike the opportunity to combine traditional durability with modern efficiency and sustainability.