The Rise of Laminated Steel in Modern Packaging
In today’s competitive packaging landscape, fully automatic lamination line technology is transforming metal packaging with superior solutions.
Why Laminated Steel is Replacing Traditional Tinplate
The Limitations of Conventional Tinplate
- Resource scarcity: Tin is a strategic yet dwindling resource
- Cost volatility: Price fluctuations impact production budgets
- Environmental concerns: Traditional coatings contain harmful solvents
Advantages of Fully Automatic Lamination Lines
- Superior barrier properties: Perfect for food, beverages, and chemicals
- Enhanced durability: Resists corrosion better than epoxy-coated alternatives
- Production efficiency: Speeds up to 200m/min with ±1°C temperature control
- Sustainability: Eliminates VOC emissions and reduces water usage by 90%
Indian Case Study: A Mumbai-based manufacturer reduced production costs by 22% after installing a customized fully automatic lamination line optimized for local spice packaging needs.
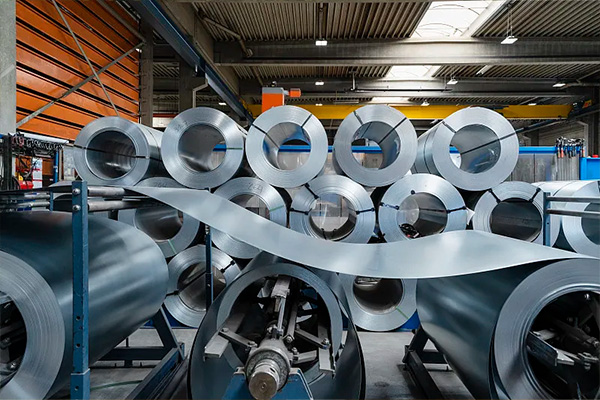
Technical Breakthroughs in Laminated Steel Production
Core Components of Modern Lamination Systems
- Precision heating: Electromagnetic induction rollers (250°C±1°C)
- Multi-layer film application: PET/PP composites (12-25μm)
- Automated quality control: Real-time defect detection
Material Innovations Driving Change
Material | Benefit |
---|---|
Chromium-plated steel | 50% cost reduction vs tinplate |
Modified PET films | Withstands 121°C sterilization |
Eco-friendly adhesives | BPA-free, FDA-compliant |
Market Applications and Growth Potential
Emerging Packaging Solutions
- DRD/DI cans: Growing 15% annually in Asia
- Easy-open ends: 50% cheaper than aluminum alternatives
- Specialty containers: Pharmaceuticals, premium foods, cosmetics
Environmental Advantages
- 73% lower carbon footprint vs traditional cans
- 100% recyclable without quality loss
- Zero wastewater in production
The Future of Lamination Technology
With global laminated steel demand projected to grow at 7.2% CAGR, fully automatic lamination lines will enable:
- AI-powered predictive maintenance
- Bio-based polymer films
- Smart packaging integration
- Energy recovery systems
Industry Forecast: China’s laminated steel capacity will triple by 2025, with India becoming the second-largest adopter in Asia-Pacific.
Cost-Effective Laminated Steel Production Line for Oil Drum Manufacturing in Russia
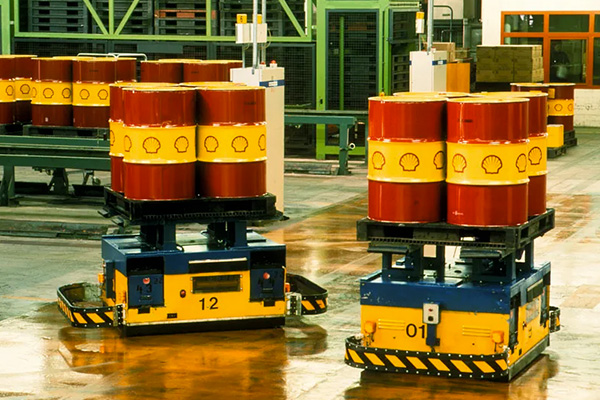
Client Profile: A leading industrial packaging manufacturer in Russia, specializing in 200L oil drums for chemical storage, required an upgrade from traditional tinplate to laminated steel to meet stringent durability and corrosion resistance demands.
Solution: We delivered a high-efficiency laminated steel production line tailored for oil drum production, featuring:
- Enhanced Corrosion Resistance: 0.3mm chromium-plated steel with specialty PET film (acid/alkali-resistant)
- Extreme Cold Adaptability: Hydraulic system optimized for -50°C startup, heated pressure rollers
- Drum-Specific Design: Precision edge-forming for 1.2-1.5mm thick steel sheets
- Localized Support: On-site Russian engineering team